It is well known that lasers have functions such as cutting, drilling, scribing, welding, and cleaning in the field of precision machining. For the automotive industry, laser cleaning is as indispensable as all other functional applications of lasers.
Laser cleaning can replace the traditional cleaning methods of pre-welding and post-welding, perform precision cleaning on the welded metal parts or welded metal parts of automotive parts, and remove paint from repair parts in the automotive aftermarket, achieving customer satisfaction in the automotive manufacturing market.
The principle of laser cleaning is mainly to peel off the rust layer on the metal surface while the laser is irradiated on the metal surface, because our laser will generate a high-intensity shock every second, which will shatter the peeled rust layer, thus completing the cleaning. As long as the correct parameters are adjusted, we can achieve zero-damage cleaning without harming the substrate itself.
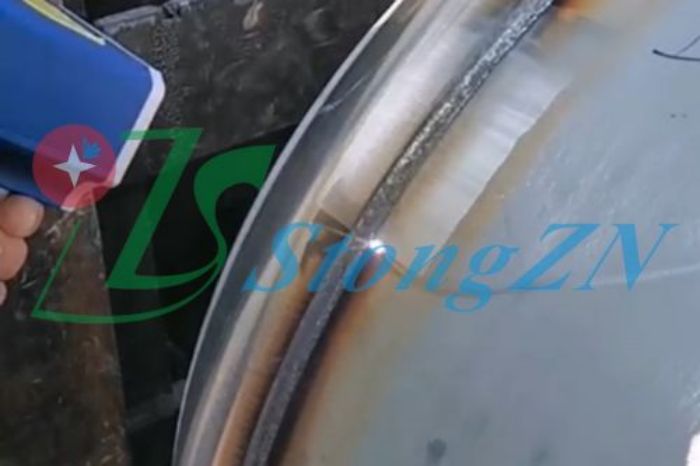
Traditional cleaning methods such as manual cleaning, pickling, shot blasting, and sandpaper grinding not only pollute the environment, but also fail to achieve automation, which is labor-intensive and time-consuming, resulting in a waste of human resources.
For example, critical welds on painted structural parts must be de-coated for inspection, such as using hand or power tools, abrasives, or chemicals, which can hide the problem area and cause further damage to the surface.
Laser cleaning has many advantages, such as no contact, no damage to the substrate, green environmental protection, fast cleaning, automation, etc. In the processing of automotive parts and vehicle manufacturing, the laser light source is used to accurately locate the oxide skin and other surface residual contaminants before and after welding of galvanized sheet and aluminum alloy, and thoroughly clean them to obtain strong, void-free and micro-crack welding and bonding, which can effectively improve the welding quality of the product.
Depending on the application, the pulse frequency, energy and wavelength of the laser must be precisely selected to clean, polish and ablate the target material. At the same time, any form of damage to the substrate material must be prevented.
The application of laser cleaning machines for polishing, surface cleaning and coating removal in the automotive industry is expanding rapidly. In addition to the automotive industry, laser cleaning is also used in mold casting, precision instruments, shipbuilding, transportation and other industries.