When it comes to molds, many people are easy to understand. From small batch cake impressions to large molds for various industrial products, injection molding, die casting, stamping, stretching, and other initial product molding are completed by molds. It is the carrier and support for the production of large-scale industrial products. China has the largest manufacturing industry in the world. Each industrial product has many styles and requires different molds. There are millions of molds in China. Some molds will be scrapped, but new molds are also opened every day. It can be said that the mold industry is an important support for China's manufacturing industry.
Since molds often come into contact with high-temperature raw materials or deal with stamping tensile stress, most molds are metal molds, and the most commonly used are various alloy steels or die steels.
Now the precision requirements of making molds are getting higher and higher. Some are composed of concave and convex sets, especially some products with convex and engraving. The molds should also be very delicate, which requires numerical control machine tool milling, drilling, grinding, etc. Instead, laser cutting is not used. If there is an error in the accuracy of the mold, it will directly lead to the forming work in progress into waste products, which not only wastes materials, but also brings huge losses to the enterprise.
In actual use, molds also have some problems that need to be solved, the most important of which is the cleaning of mold residues, and there is no good solution so far. Some metal molds are used for the molding of high-temperature hot melt materials, as well as the die-casting of some metals. After the product is completed and taken out, there are often raw materials left on the mold, which will directly affect the continuous production of the next product, and even require downtime for manual cleaning of the mold, resulting in missed work.
The second problem is the rust cleaning of molds. Most industrial molds are metal steel, and many molds are temporarily put on hold or in the spare stage after use, often rusting. Since the molds must be cleaned before they can be used on the machine, traditional cleaning requires a lot of labor, which brings great cleaning trouble to the manufacturer.
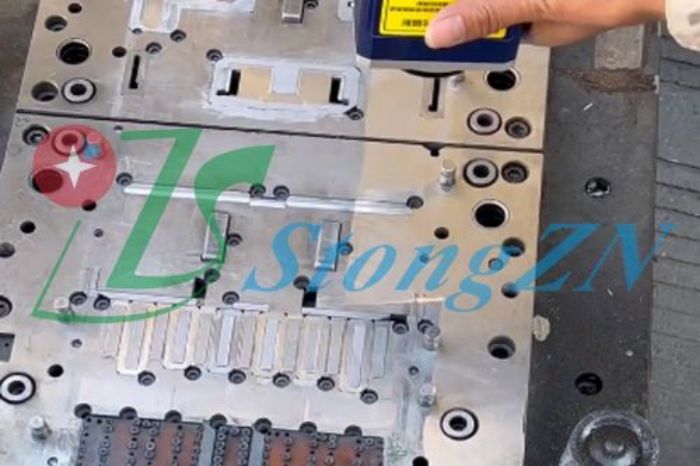
The principle of laser cleaning is to use the high energy and high frequency beam of light of the laser to hit the surface of the workpiece, so that the surface residue, rust, dirt, oil, etc. are instantly peeled off the surface of the workpiece. Anyone who has seen the laser cleaning effect knows that as long as the laser beam is swept, the surface will be swept clean in a few seconds.
At present, laser cleaning can effectively clean planes, curved surfaces, holes and gaps. The use of common hand-held laser cleaning machines is more than enough to deal with the rust of general metal molds, and the cleaning time may only be one-tenth of that of traditional cleaning. Another is to deal with the raw material residues on the molds, especially the molds on the production line. The efficiency of manual digging is relatively low. If you replace it with laser cleaning, the efficiency is much higher. If you can synchronize laser cleaning to the mold production line, monitor and automatically clean the residual raw materials on the molds, you can solve the problem of long downtime delaying production.