As a new type of cleaning technology developed in recent years, laser cleaning has many advantages over traditional cleaning technologies. Laser cleaning has the characteristics of non-grinding, non-contact, non-thermal effect, and is suitable for objects of various materials. It effectively removes rust, oil, film, oxide skin, paint, and other contaminants on the surface of the object without damaging the substrate.
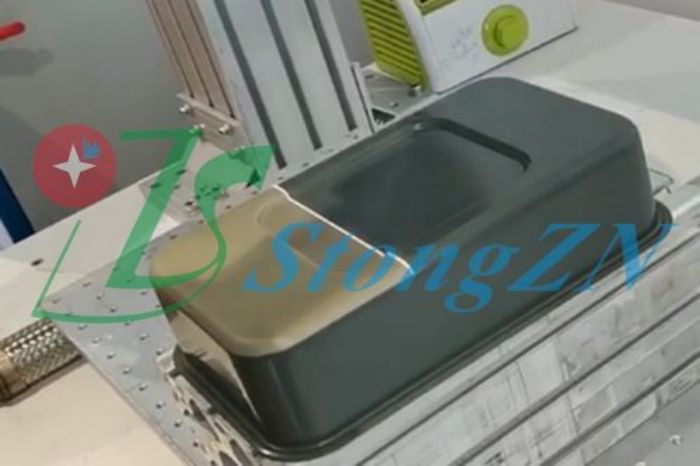
No contact with the surface of the object during laser cleaning
The traditional cleaning method is often contact cleaning, which has a mechanical force on the surface of the cleaned object, damages the surface of the object or adheres to the surface of the cleaned object, and cannot be removed, resulting in secondary pollution. The non-abrasive and non-contact nature of laser cleaning makes these problems easy to solve.
No damage to the surface of the object during laser cleaning
Laser cleaning can remove various types of contaminants from the surface of various materials, achieving cleanliness that cannot be achieved by conventional cleaning, and can also selectively clean the contaminants on the surface of the material without damaging the surface.
Laser cleaning allows for precise positioning
The use of fiber-optic transmission to guide the laser, in cooperation with robotics and robots, facilitates long-distance operation, and facilitates non-contact laser cleaning of corners that are difficult to reach by traditional cleaning methods, such as special-shaped parts, holes, and grooves. This can effectively ensure the safety of personnel in some dangerous places.
The laser cleaning process is pollution-free
Laser cleaning does not require chemical cleaning agents and does not generate cleaning waste liquid. The pollutant particles and gases generated during laser cleaning can be simply collected and purified by a portable exhaust fan to avoid environmental pollution.
Low operating cost of laser cleaners
The laser cleaning system can be used stably for a long time. The laser used in the laser cleaning machine has a long service life, no consumables are consumed during use, and the operating cost is low. The lens needs to be cleaned or replaced regularly in the later stage, which is close to maintenance-free.
As a laser cleaning technology suitable for industrial production, it is an indispensable process in the production process, such as weld treatment before and after welding, local dirt treatment before painting, and oxide cleaning in the production of highly active metals.