Laser cleaning is known as "the most promising green cleaning technology in the 21st century." With the acceleration of industrialization and the steady advancement of the "double carbon" goal, it has gradually replaced traditional cleaning processes in many fields, and has gradually become an indispensable equipment manufacturing technology in high-end manufacturing fields such as industry, rail transit, ships, and aerospace.
The concept of laser cleaning originated in the mid-1980s. Its principle is to use high-frequency short-pulse laser as a cleaning solution for the working medium. The specific wavelength of high-energy beam of light is absorbed by the rust layer, paint layer, and pollution layer, forming a rapidly expanding plasma (highly ionized unstable gas), and at the same time generating shock waves, which turn the contaminants into fragments and remove them. It can stably and effectively clean the surface of various substrates, including metals, alloys, glass, and various composites.
The application of laser cleaning in the new energy industry
At present, laser cleaning has become the main means of surface treatment in the new energy industry, and is widely used in the production process of new energy vehicle bodies, parts, pre-welding and post-welding cleaning. By using lasers, cleaning heads and control software, computer integrated control greatly improves the level of manufacturing technology.
1. Laser cleaning of new energy vehicle bodies
The main application of laser cleaning technology in the new energy vehicle body is the cleaning operation before welding and after welding. The cleaning before welding can effectively remove oil impurities and effectively avoid welding pores. The cleaning of the weld after welding can remove post-welding oxides, welding slag, and other impurities. The welding strength and elongation are greatly improved, the welding uniformity is strengthened, and the welding quality and appearance are improved.
2. Laser cleaning of new energy components
Using a laser cleaner to clean automotive liquid-cooled tube components can quickly clean the surface of flux oil and other residues, improving product quality. Experiments have shown that the effect of laser cleaning is significant, and the product qualification rate is increased by 20%.
3. Laser local cleaning of battery components
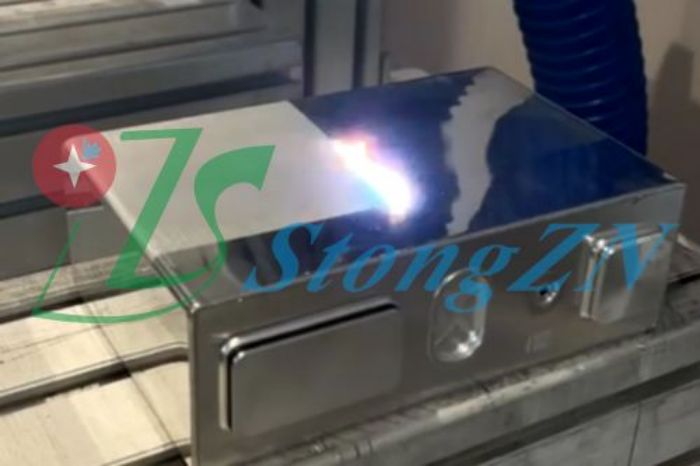
Laser cleaning technology is applied to the cleaning of specific parts such as battery components. It has the characteristics of strong positioning and good directivity. It can focus the beam of light and concentrate the beam of light into a small area to achieve excellent cleaning effect. After cleaning, the surface has no scratches and burrs, thereby improving the safety performance and service life of the power battery.
Shengtong intelligent laser cleaning machine is suitable for surface cleaning of various components in the new energy industry. It can be localized to achieve precise and precise cleaning, and perfectly solve cleaning problems such as oxidation, oil removal, metal particles, dust, etc. At the same time, laser cleaning can realize automated cleaning, batch cleaning, and cleaning efficiency is higher and faster. This is the ideal choice for cleaning in the new energy industry.
The new energy manufacturing process requires high quality consistency and higher precision in process control. Shentong Intelligent Laser will continue to explore user cleaning needs, help users solve cleaning technical problems, and promote the development of laser cleaning in the new energy industry with technical hard power, and promote the further expansion of the laser cleaning market.